Full Inventory Counts Are Costing You Money
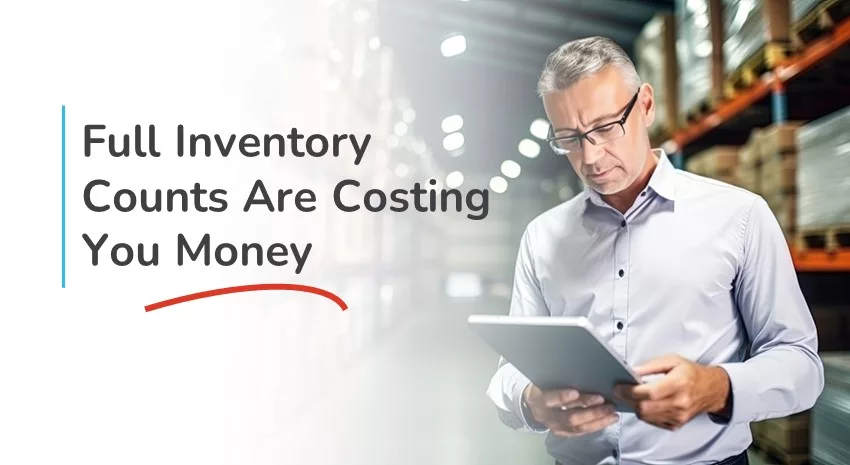
Inventory counts typically make up the biggest balance sheet asset because their accuracy is key to calculating profitability and offering effective customer service. Performing physical inventory counting takes up time and money that could be invested into production, distribution and sales instead.
Shrinkage is also one of the big risk factors that cost companies when performing full inventory counts. Cycle counting processes and inventory management can simplify things and save companies on the costs of talent and loss of open time.
The importance of accurate inventory information
Accurate inventories are critical for calculating the cost of goods sold, an essential component of preparing the company’s balance sheet and earnings statement for investors. Inaccurate numbers can lead to fines, penalties, and a lack of investor confidence.
Maintaining an accurate count of your physical inventory is also important to businesses by identifying:
- Discrepancies between the inventory tracking system and physical inventory.
- Where inventory is overstocked, which represents an unnecessary expense and waste.
- Where inventory is understocked, which can potentially lead to items being out-of-stock and customer dissatisfaction.
- Areas where the inventory of popular or high-value items is significantly lower than should be in stock, indicating shrinkage through theft, breakage, clerical errors, etc.
- Items that are moving vs. those that are not, critical for stock replenishment decisions.
What is counted?
Counting physical inventory includes all your warehouses, store shelves, manufacturing floor, third-party warehouse locations, and items being returned or in transit between warehouses and stores.
Counting teams work in pairs, with one person conducting the count and the other recording the information, including item description, quantity, part number, warehouse/bin location, and unit of measure.
How is the count conducted?
Four of the most common methods for conducting inventory counts are full (or periodic) counting, cycle counting, tag counting, and ad hoc (or spot) counting.
In a full inventory count, the company sets aside several days to conduct a complete count of every item in inventory across all their warehouses. Businesses often suspend incoming and outgoing deliveries to ensure the count is accurate.
Items are separated on arrival, so the ongoing count is not affected. Full counts require a significant amount of time and staff to complete. They often require operations to be suspended for the duration of the count, which can significantly impact the business.
Because of the massive effort, full inventory counts are conducted only once or twice a year. Any discrepancies in warehouse management software, evidence of theft, or replenishment problems might go unnoticed for a year before the issue is raised to management.
Inventory counting method: Which is best?
While full counts are most straightforward to understand and conduct, they are labor intensive, error-prone, and require that operations be suspended until completion.
For many companies, cycle counts are the most efficient. Rather than conduct a single, massive inventory count, the inventory is counted in pieces distributed over a specified time period, minimizing the impact on the company and allowing the business to continue operations. Once completed (say in four months), the cycle can be repeated repeatedly. Because cycle counts are ongoing, they can uncover problems like fraud, theft, or poor training.
Cycle Counting Methods
Cycle counts break the inventory up into groups by type or location. The count team only counts the items in a specified group. This means that the count team might be only two people spending several hours daily performing inventory counts over weeks or months. They focus on counting only the items in a specific group each day.
Cycle counts are less impactful on the organization because they do not require shutting down all operations for the duration of the count. It can also be conducted by a handful of people for a specific time range, usually a quarter.
Variations in how a cycle count is conducted focus on the type of item assigned to be counted next.
- The ABC, 80/20, or Pareto method: This popular cycle count method uses the Pareto Principle, which states that 20% of the items in your warehouse are responsible for 80% of your sales (usually because they are the most popular or most expensive items). In ABC cycle counts, items are assigned a letter (A, B, or C) based on their sales frequency or value. A, the most frequently sold/most valuable items are inventoried more often than Bs, which, in turn, are inventoried more frequently than Cs.
- Grouping by warehouse location or Bin Counting: This method simplifies the counting process by assigning the next group to be counted in bins in the same vicinity as the others.
- Random grouping: The items to be counted are selected at random.
Pros of cycle counting:
- Removes the need for stressful annual counts
- Enhances the quality of reports because it’s easier to plan and strategize
- Helps identify potential bottlenecks and deal with them at an earlier stage
Cons of cycle counting:
- Risk of miscounting when setting the counting orders, which ripples into several possible errors
- Employees are required to count more often, which could lead to more distraction and mistakes
- Restricted to counting before opening hours because goods counted as part of the orders in open hours could be sold before being counted as part of the cycle
Ad-Hoc Counting
Ad-hoc or spot counting is often used when there is a question about the inventory count in one area, even if it was recently counted. Count teams are assigned a designated area or item list. Once they complete it, they update the information in the warehouse management system.
Since ad-hoc counting is usually unscheduled, it’s important that your system has the capability to match the quantity that has already been counted against the amount that exists in the software. This method is typically used in small warehouses or stores.
Pros of ad-hoc counting:
- Enhances flexibility of counting when handling previous errors or emergencies
- Improves accuracy by allowing for adjustment of cycle count scheduling
- Empowers employees by creating easier access and filing capabilities
Cons of ad-hoc counting:
- It relies on employees to identify when to perform ad-hoc counting, which leaves room for human error
Tag Counting
For tag counting, every item in inventory is given a tag. Count teams fill in the item count and information. At the end of the count, the tags are collected and entered into the system. Tag counting stands out from the other methods because it doesn’t require an immediate comparison against the software data. It’s like creating a preliminary draft list then adjusting it according to sales and then building another counting order to match it against.
Pros of tag counting:
- Simplifies the tracking process for stores with no single storage location because the tags provide a visual cue of what is and isn’t counted for
- Saves time since counting can be done during opening hours
- Offers unmatched transparency
Cons of tag counting:
- Tag counting isn’t the most effective method for all businesses.
Optimize Your Inventory Management
Using an optimized inventory management system helps maintain accurate and easily accessible stock in all locations. If you need help getting your inventory under control, contact us. ArcherPoint’s inventory management experts will evaluate your situation, recommend process improvements, and help you optimize Business Central for your unique inventory management requirements.
Trending Posts
Stay Informed
Choose Your Preferences
"*required" indicates required fields