Understanding the Differences Between MRP and MPS
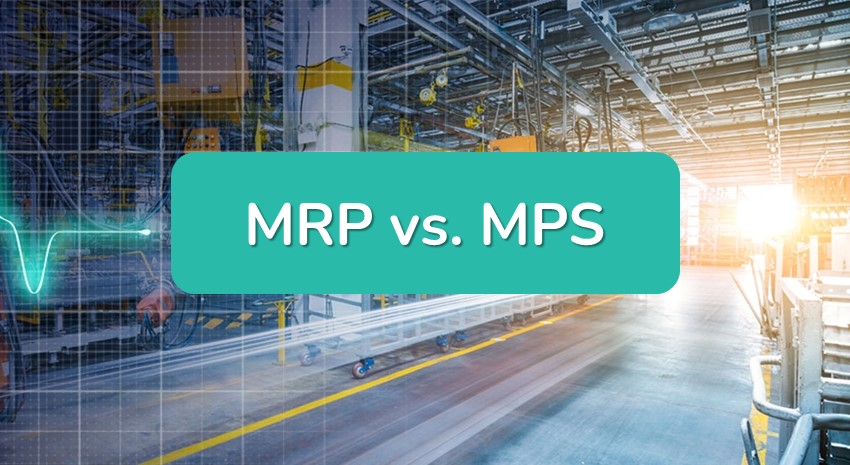
The main difference between master production schedule (MPS) and material requirements planning (MRP) is that MPS defines the number of products to manufacture and by what date, while MRP details the materials needed to create those specific products by the deadline. The MRP stage is conducted to match the needs of the MPS.
This article explains more about the differences between the two processes:
What Is an MPS?
A master production schedule helps manufacturers plan which products and how many to produce for a certain period. It’s a proactive technique that helps companies prepare for upcoming seasons. The main goal of an MPS is to align sales demand with manufacturing capacity.
MPS gives companies a realistic blueprint of what they can expect, which prevents overstocking. It also improves customer service by allowing businesses to manufacture products on time, which prevents delivery delays.
How Does an MPS Work?
An MPS works by planning which products should be manufactured, by what date, and in what quantities. Once it’s complete, the MPS forms the foundation for drawing lines of communication between sales and manufacturing. It prevents instances where sales may make promises that production can’t keep, which leads to unhappy customers.
One feature that makes an MPS so efficient is its flexibility. You can adjust it at any time to meet changes in demand.
What Are the Benefits of an MPS?
Creating an MPS provides many benefits for companies of all sizes and industries. The main perks are that it increases profitability and reduces shortages. Here’s a breakdown of the top benefits businesses can expect upon implementing an MPS:
- Simplifies order promises: The MPS ensures everyone knows how long it’s expected to take to create a product by providing buyers with accurate lead times. It also prevents utilization-dependent exhaustion that may occur due to work intensity.
- Enhances communication: An MPS acts as a communication tool that helps manufacturing share information about production plans with the other departments. It improves transparency and visibility, especially between sales and manufacturing.
- Boosts efficiency: An MPS provides a means to analyze and solve potential bottlenecks by using available resources to meet deadlines. In the long run, this improves customer satisfaction and sales.
- Streamlines supply chain: An MPS reviews the supply chain requirements and arranges them in priority order, which boosts supplier relationships by ensuring timely delivery.
When Should You Create an MPS?
An MPS typically runs at consistent times to adjust the output regularly based on production orders. Many businesses perform it at the three-month mark, while some make it two years out. To determine when is the right time for your company to create an MPS, consider the following factors:
Is there an amount of stock you’ll want to keep as a backup so you don’t run out of inventory?
How much inventory do you have in stock already?
What does the sales forecast say about the amount of orders expected for the upcoming time frame?
What are the orders you already have planned?
What amount must be produced to create a balance between supply and demand?
Should You Use MPS Software?
MPS software is perfect if you want to make the scheduling process as easy, convenient, and valuable as possible. Specialized software like Microsoft Dynamics 365 Business Central helps align work centers with store calendars and capacity, which prevents errors during MPS processes.
This software allows you to easily extract capacity data and schedule anticipated orders. It allows for manual adjustments when a company may need to alter specific objectives, but it also offers automatic scheduling for convenience. You can override planned production levels with scheduled levels, and the software automatically recalculates them to suit the current conditions.
MPS software also enables you to view visual representations of the production schedule through graphs. You can simply click and drag the desired points on the graph to alter the production schedule or move specific items.
What Is an MRP?
Material requirements planning has existed for almost 50 years and isn’t going anywhere. MRP helps companies determine what materials are needed and in what quantities to meet the MPS for a target period. It’s primarily done via specialized software that helps businesses access the proper inventory during specific production processes.
MRP is essential for worker productivity, flexibility, and efficiency within the manufacturing plant. It helps businesses respond quickly to sudden increased demand while minimizing labor and material costs. This process improves customer satisfaction by reducing delays, which has a ripple effect on revenue growth.
What Are the Benefits of MRP?
MRP offers many benefits to businesses of all sizes. Its ability to automate inventory management and complex calculations allows companies to scale up in ways that wouldn’t be possible without it. Here are the top benefits MRP offers organizations:
- Boosts production efficiency: MRP gives managers significant insights into the time and supplies needed to keep production flowing smoothly. It allows them to track and use raw data to minimize delays and miscalculations.
- Reduces purchasing costs: This process automates searches and allows businesses to access the most cost-effective solutions. By minimizing purchasing costs, companies can offer better product cost-efficiency and reap the bottom-line benefits.
- Implements emergency strategies: MRP helps ensure efficient management of stock. It sets strategies to prevent excess inventory by ordering when it needs replenishing. You can also maintain safety stock in case of emergencies.
- Prevents common production bottlenecks: This software allows businesses to create an uninterrupted production flow by identifying potential bottlenecks before they occur. It helps management proactively monitor the fluctuating demand and identify material scarcity to prevent halting production.
- Improves inventory control: Supply chain management becomes easier with MRP processes. They use real-time data to display current supplies readily. This convenient feature allows managers to identify any materials that need replenishment before they run out. It prevents disruptions in the manufacturing process and improves customer satisfaction.
How Does MRP Software Work?
MRP works by defining Dependent vs. Independent Demand to decide which items fit into the program. Independent Demand comes from outside the company. Dependent Demand is what is required to create a specific item that the final product needs. It typically comes from upper-level requirements, and it’s essential for keeping the production schedule together.
This software converts the plan from the MPS to a list of parts, raw materials, and other supplies needed to create the final product amount. MRP software helps manufacturing managers determine the quantity of supplies and labor required to achieve production efficiency and deliver on the MPS.
Here are some of the typical data that managers would input in the MRP software to improve efficiency:
- MPS
- Item name or level
- Inventory status file (ISF)
- Shelf life of items in inventory
- Quality testing standards and labor and machine standards
MPS vs. MRP: What’s the Difference?
The key difference between MRP and MPS is that MPS concerns the quantity needed to meet demand, while MRP concerns organizing the materials and labor required to create the desired amount.
The MPS is the driving force behind the MRP because it uses a bill of materials (BoM) to help managers find the missing resources and labor. Together, MPS and MRP help organizations reach new heights of productivity, efficiency, and return on investment.
Increase Business Efficiency With ArcherPoint
At ArcherPoint, we specialize in world-class enterprise resource planning (ERP) and cloud solutions that streamline and simplify every step of your manufacturing, sales, and customer service portals. We are a certified Microsoft Dynamics ERP Solutions Partner for Business Applications, a full-service Dynamics 365 Business Central provider, and a Cloud Solution Provider (CSP).
Our experts can provide the support and development your company needs to work easier and smarter with the latest in Microsoft and Cloud solutions. Don’t hesitate to contact us and reap the benefits of first-rate digital system solutions now.
Trending Posts
Stay Informed
Choose Your Preferences
"*required" indicates required fields