Managing Space Utilization: Overcoming warehousing challenges in 3PL operations
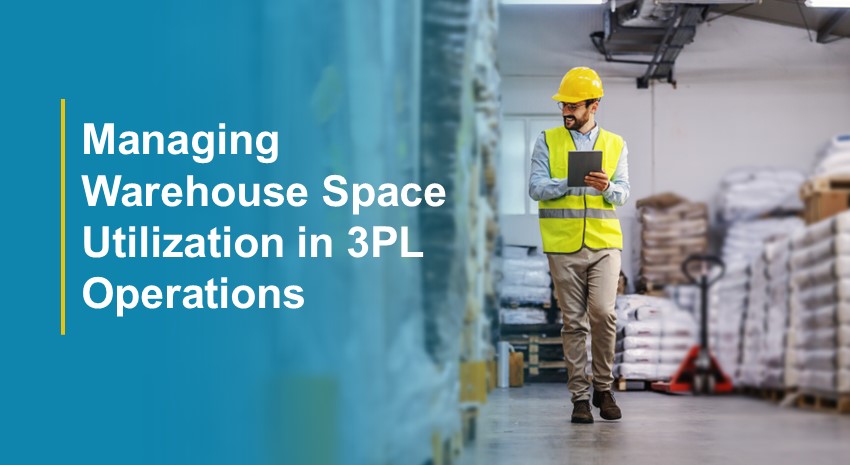
For third-party logistics (3PL) companies, efficient space utilization is a key driver of operational success. While often viewed as a logistics business, 3PL is fundamentally a real estate business—focused on acquiring commercial storage space, segmenting it into pallet-sized units, and renting it out for maximum profitability. Success in 3PL depends on optimizing warehouse space, selecting strategic warehouse locations, and maintaining competitiveness through operational efficiency.
Warehousing is one of the most significant cost factors in 3PL operations. Underutilized or inefficiently used space can lead to increased expenses, lower productivity, and reduced service quality. Unlike distributors who aim to streamline inventory levels, 3PLs thrive on increasing inventory to fully utilize their storage facilities. Managing space effectively is a complex challenge given the dynamic nature of logistics.
Key space utilization challenges in 3PL warehousing
Real estate considerations and strategic location planning – Just like in real estate, 3PL success is heavily dependent on location. Proximity to major transportation hubs—highways, airports, seaports, and trucking routes—ensures efficient movement of goods. Strategic positioning allows for optimized flow of inventory and improved service to customers. Understanding traffic lanes and the density of competing 3PL warehouses along those routes is crucial when selecting warehouse locations.
Seasonal inventory fluctuations – 3PLs must manage drastic variations in inventory throughout the year. Certain warehouse types, such as cold storage facilities, tend to remain resilient in downturns because food and beverage products maintain demand regardless of economic conditions, whereas sectors driven by consumer demand (e.g., retail during the holidays) experience peaks and valleys in space requirements.
Warehouse layout and slotting inefficiencies – Inefficient warehouse layouts waste valuable space and slow down operations. Proper slotting strategies—such as placing high-moving inventory closer to docks—can reduce travel time for workers. Additionally, advanced warehouse designs, including automated vertical storage, can increase pallet density without requiring additional square footage.
Dock congestion and inefficient staging areas – Poorly managed inbound and outbound shipments lead to dock congestion and inefficient staging. This bottleneck disrupts workflows and increases labor costs. Optimized scheduling and staging areas improve loading and unloading times, preventing warehouse slowdowns.
Underutilization of vertical space – Many 3PL warehouses fail to maximize their vertical storage capacity. In regions with limited land availability (such as Europe), automated vertical warehouses with robotic cranes are common. North American warehouses should also consider vertical storage solutions to enhance space efficiency.
How 3PLs optimize warehouse space utilization
Dynamic slotting and warehouse layout optimization – AI-driven WMS solutions optimize slotting in real time. Optimized slotting reduces travel time and increases warehouse throughput.
Implementing high-density storage solutions – 3PLs use innovative racking and storage systems to increase capacity without expanding their footprint:
- Push-back and drive-in racking: Reduces aisle space and stores multiple pallets deep.
- Vertical lift modules (VLMs): Automates vertical storage to maximize cubic space.
- Mezzanine floors: Creates additional storage levels within existing facilities.
Cross-docking to minimize storage needs – Cross-docking reduces the need for long-term storage by facilitating the direct transfer of inbound shipments to outbound transportation.
Optimizing dock scheduling and staging areas – Digital dock scheduling tools streamline inbound and outbound logistics. Efficient staging prevents congestion and enhances warehouse productivity.
Leveraging automation and AI for space management – Automated Storage and Retrieval Systems (AS/RS) and AI-powered demand forecasting optimize warehouse space dynamically. These solutions reduce manual labor costs and increase storage efficiency.
The role of flexibility in 3PL operations
Flexibility is a critical competitive advantage for 3PL providers. In economic downturns or when tariffs disrupt supply chains, customers reassess their logistics partners. The first 3PL company to be cut is often the one that causes the most operational challenges. To avoid being replaced, 3PLs must offer adaptable and efficient warehouse solutions tailored to their customers’ needs.
How Boltrics helps 3PLs manage warehouse space efficiently
Boltrics’ WMS is designed with adaptability in mind. Unlike rigid logistics systems, Boltrics provides:
- Customizable workflows – Adjust operations based on customer requirements.
- Automated administrative and operational tasks – Reduces inefficiencies and labor costs.
- Seamless web portal access – Enhances customer transparency by providing real-time inventory visibility.
By focusing on flexibility, automation, and efficient warehouse management, Boltrics helps 3PLs enhance space utilization, maintain high service levels, and ensure long-term profitability—even during economic uncertainties.
Find out more
3PL operations are fundamentally real estate businesses that depend on warehouse space utilization, strategic location selection, and operational efficiency. Unlike distributors, 3PLs must maximize storage occupancy while optimizing logistics. Advanced warehouse management strategies—such as AI-driven slotting, high-density storage, automation, and proactive inventory management—allow 3PLs to remain competitive and profitable.
Investing in a flexible WMS solution like Boltrics ensures that 3PL providers can adapt to market fluctuations, improve operational efficiency, and retain customers by providing seamless and transparent logistics services. Efficient warehouse space management isn’t just about maximizing storage—it’s about driving profitability and long-term success.
Contact the 3PL experts at ArcherPoint and learn how Boltrics can help your company manage warehouse space utilization and be more competitive.