Using Standard Costs in Dynamics NAV
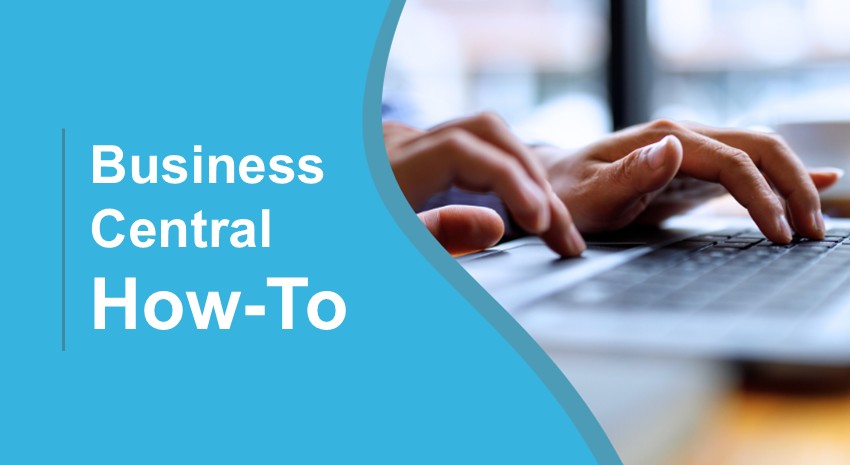
NOTE: This blog applies to any version of Microsoft Dynamics NAV, including NAV 2016. The screenshots are taken from NAV 2013.
To begin a discussion about setting up time using standard costs in Microsoft Dynamics NAV, we must first examine the dilemma of trying to include setup as part of the āDirectā cost of an item.
Setup is a one-time cost; it is not a cost that reoccurs for each piece that is produced. So the question is, how do you split the one-time cost and assign each item that is produced as part of the setup cost?
That is a somewhat rhetorical question. The only way that this can be done is to make an assumption about how many pieces will be run when you set up to run this item. If you always run 100 pieces when you set this item up, for example, then it makes sense to divide the setup time by 100 and assign 1/100th of the setup cost to each item. The problem is, rarely do companies run the exact same quantity each time they setup to run an item up. My guess is that this varies on an order by order basis.Ā
So letās take a look at how to handle setup time in NAV when using Standard Cost as the costing method.
There are really two choices for you to consider when you think about including setup time in your cost of the product.
- Include as a āDirect Costā
- Include as anā Overhead Expenseā
There is no right or wrong way to handle setup expenses. Both are acceptable and provide valid costing based on the assumptions you make. The sections below take each of these options and walks you through how you would use NAV to include the setup costs based on the assumption you move forward with.
Before detailing how to set up the setup costs in NAV, letās review the circumstances where one option seems to make more sense than the other.
- When using Standard Costing, there is a basic assumption that your costs are predictable and repeatable. This means that your purchase price is fairly consistent, your production process is consistent, and therefore, your costing is consistent. The assumption is that any variance to your production rate and costs are small and therefore recognized as a monthly operating expense rather than the cost of the item.
If your production run size is pretty consistent when you set up to run an item, then using Setup as a direct cost makes sense. This means that the run size difference from order to order is a very small percentage to the size of the production run.
- If the run size varies significantly from order to order, then the base assumption that the cost is predictable is not necessarily valid. Large swings in the run size from order to order mean the setup cost per unit is significantly different and therefore may be more appropriate to consider as an overhead expense. Considering setup as an overhead cost means that you would estimate all the setup costs for the year and then spread all overhead costs over each piece that is made in that work center. By making it a global estimate, the average for all pieces is more accurate than the order by order difference per part.
Standard Costs Setup as Overhead
When applying setup as overhead, two things need to be estimated by work center:
- Total setup costs for the year
- Total production run time for the year
Dividing the total production run time for the year into the total setup costs for the year would calculate the setup cost per hour that should be absorbed with each hour of production through that work center. This rate would then be added to the other overhead expenses that are associated with that work center and included in the cost of the item. This value would be populated in the Overhead Rate field on the Work Center card.
In the example below, the work center is set up to track production in hours. The Overhead Rate field is the amount of overhead expense that is applied for each hour of Run Time on production routings for this Work Center.
Figure 1. Work Center set up to track production in hours.
Standard Costs as OverheadĀ
Letās walk through an example of how setup costs would be absorbed as an overhead expense.
In our example, the following conditions are true for our Machining Work Center:
- Production runs 250 days a year
- There is typically 1 setup done per day
- The average setup time at this work center is 30 minutes
- The expected total setup time for the year = 250 * .5 = 125 hours
- The setup hourly wage is $20 per hour
- The total Setup Cost for the work center is 125 Hours * $20 per Hour = $2500
- Production runs 1 shift 6 hours a day (1-hour setup, 1-hour breaks and lunch)
- Total production run time for the year is 250 * 6 = 1500 hours
- Setup Cost per hour of production run time is $2500 / 1500 = $1.66667 per hour
The $1.66667 per hour would be added to the other overhead costs per hour, and loaded into the Overhead Rate field on the work center card.
Standard Costs Setup as a Direct Cost
An average setup cost per unit must be determined if the setup cost will be included as a direct cost of the item. This means that NAV must be able to calculate this average cost per unit. This is done by defining three things:
- Setup Time for an item
- Cost per hour
- āNormalā quantity produced per run
These three important fields are stored in different places in NAV. The sections below define where these key pieces of information are stored.
Setup Time
The setup time is defined on the routing for the item being built. Each routing operation could have a setup time assigned to it.
Figure 2. Setup Time.
Cost per Hour
The cost per hour is the work center cost fields. The value of the cost per hour is determined by the cost fields on the work center. These fields are the:
- Direct Unit Cost
- Indirect Cost %
- Overhead Rate
Figure 3. Work Center card with work center cost fields highlighted.
These fields are totaled in the Unit Cost field. The Unit Cost field is the Cost per Hour (whatever the scheduling unit of measure value is).
Normal Production Run Quantity
The setup cost for a production run must be broken into a cost per unit. This means there must be an assumed quantity that is being produced so that a setup cost can be calculated for each unit produced. This assumed run quantity is stored in the Lot Size field of the item card.
Figure 4: Item Card with Lot Size field highlighted.
To set this value correctly, you will need to study your production run sizes and establish your āStandard Cost Lot Sizeā for each item. Once established, you would store this value on the NAV Item Card. NAV will then divide this quantity into the Setup Time for each operation to calculate the setup time per item. The per-unit Setup Time costs would then be added to the run time costs to calculate the total labor cost for the operation.
If you study the Detailed Calculation Report for the above item, you will see how the Lot Size is used to calculate Setup Costs per item.
Figure 5. Detailed Calculation report.
Standard Costs in Microsoft Dynamics NAV: Summary
Including setup costs in Standard Costing can be tricky and generate variances on an order by order basis. Including setup time in your direct costs makes sense if your production run size for that item is consistent from order to order.
If your run sizes vary, then it may make more sense to treat setup as an overhead expense and build it into the Overhead Rate associated with the work center.
If you have any questions about this or other processes, contact ArcherPoint.
For more step-by-step instructions on how to perform specific tasks in Microsoft Dynamics NAV, see our collection of How-To blogs.
Other blogs on this topic include:
Rolling Up Standard Costs in Microsoft Dynamics NAV
ArcherPointās costing experts show how to use the Standard Cost Worksheet in Microsoft Dynamics NAV as a more reliable method to roll up Standard Costs.
Determine Actual FIFO or LIFO Value of Inventory Using Standard Cost
This blog discusses how to determine actual FIFO or LIFO value of inventory using Standard Cost in Microsoft Dynamics NAV.
Purchases and Direct Cost Applied Accounts in Microsoft Dynamics
This blog discusses Purchases and Direct Cost Applied Accounts and how they are used in Microsoft Dynamics NAV 2013.
Which Dynamics NAV Costing Method Should Manufacturers Choose?
Read about the various costing methods available in Microsoft Dynamics NAV with a special focus on manufacturing.