Best ERP Manufacturing Software
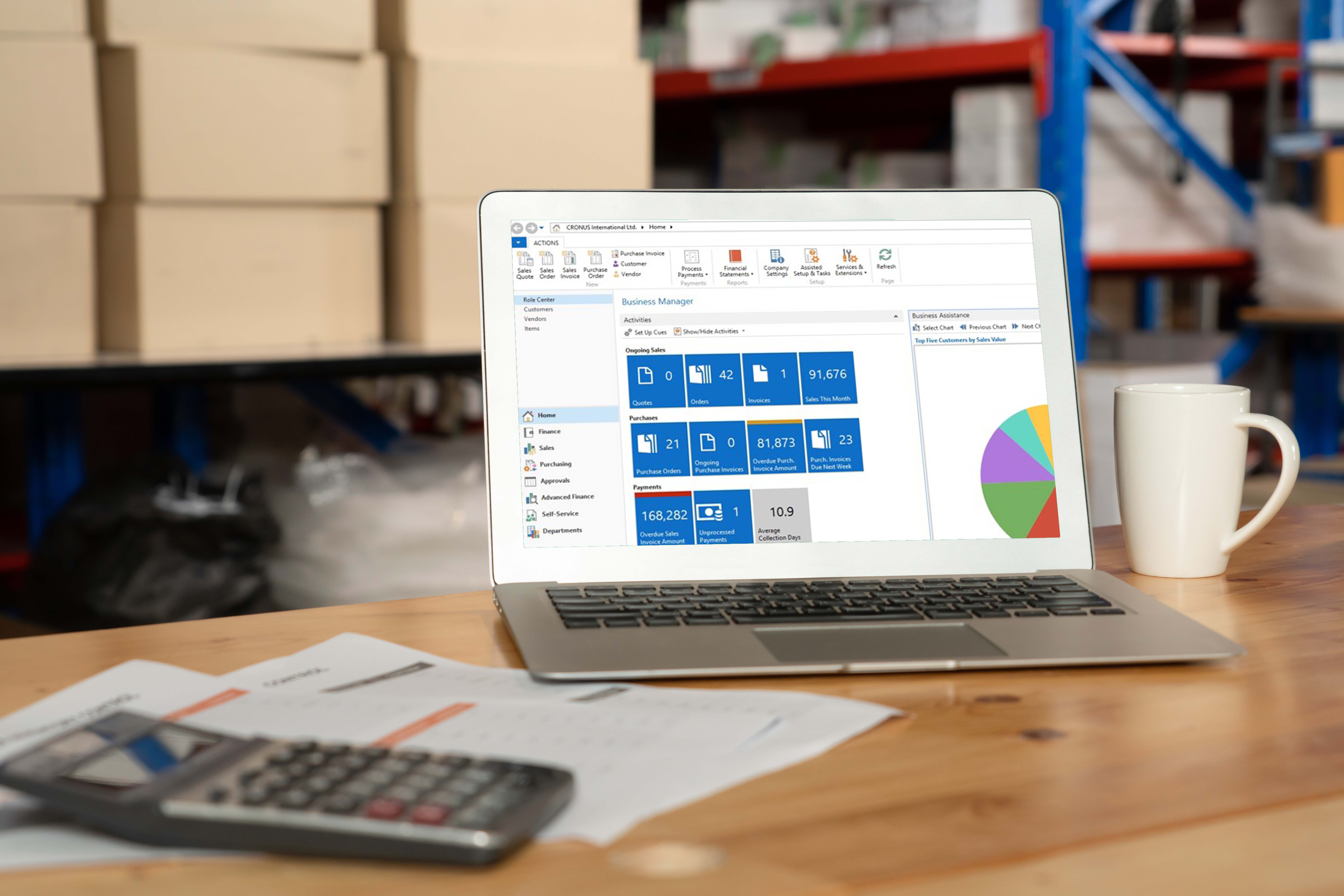
Dynamics NAV and ERP Manufacturing
Despite all the various refinements to ERP systems, including Microsoft Dynamics NAV (Navision)—advances in forecasting and internet sales ordering from smart phones, remote warehouses, “pick-up” lockers in major cities and same-day order and delivery—there are still going to be aspects of raw material warehousing, manufacturing machines, assembly lines, etc. that will need a solid, reliable, and flexible ERP system. Regardless of the product, we will still be required to move all its components or ingredients to the location where the manufacturing is taking place and deal with how the production flow will originate from raw material storage. Yes, new ERP and WMS systems assist in the control of inventory as a decoupler, but in this way, the Dynamics NAV database can be the best ERP for the Manufacturing Industry.
We can extend this from discrete to process manufacturing, where, very basically, raw materials are received from vendors, stored, issued for production, and consumed in the production operation.
Prior to this ongoing procedure, NAV and its robust features provides a virtual box of tools to assist the Manufacturing Engineer in his or her task of designing and producing a product that not only meets consumer requirements but also ensures the cost and method of manufacture is feasible.
Yes, there are CAD (Computer Assisted Design) programs, but the manufacturing engineer also comes with a box of tools derived from formal education and prior experience developing products. This experience and use of NAV tools is especially applicable to manufacturing, processing products for consumers, or any market for that matter. A great majority of new products, once conceived, require intimate, hands-on work in the design phase, use of optimum materials selection, ways of manufacture, throughput volumes, number of machine and work centers required…the list goes on and on.
Using an up-to-date copy of the production database, engineers can use the tools that are standard in Dynamics NAV including:
- Costing
- Work & Machine Centers
- Capacities
- BOMs, and Versions of BOMs
Allow of this allows for the forward development of products with the added benefit of current item, BOMS, etc., all resident in the same database.
The Costing granule is a key ingredient in identifying not only material costs but rolled-up material costs prior to management approval of the product, cost, etc.
This planning capability is not confined to the manufacturing arena. The addition of new raw materials, finished goods items and processes can be used to project increased volumetric requirements of new material storage space, unusual handling requirements, and so on. The data obtained from the NAV database can be used to drive any measure of storage, movement, manpower, etc. without, very importantly, the additional costs of purchasing additional software or expertise for short periods of planning and growth.
In addition, projected sales of the new product(s) can be processed through the NAV database to provide a view of profitability and numerous other aspects. In fact, companies intending to expand, through new production lines, plants, products, etc., can rely on the NAV database as a complete planning tool. Many EDI situations and new product flows can be tested…the list is actually endless and is only limited by the requirements of the planners.
If you have any further questions about this or other manufacturing questions, please contact one of our manufacturing and distribution experts at ArcherPoint. If you liked this, you might like to check out our eBook on Technology Trends in Discrete Manufacturing.